Plastic Mold Injection Manufacturers: The Backbone of Modern Manufacturing
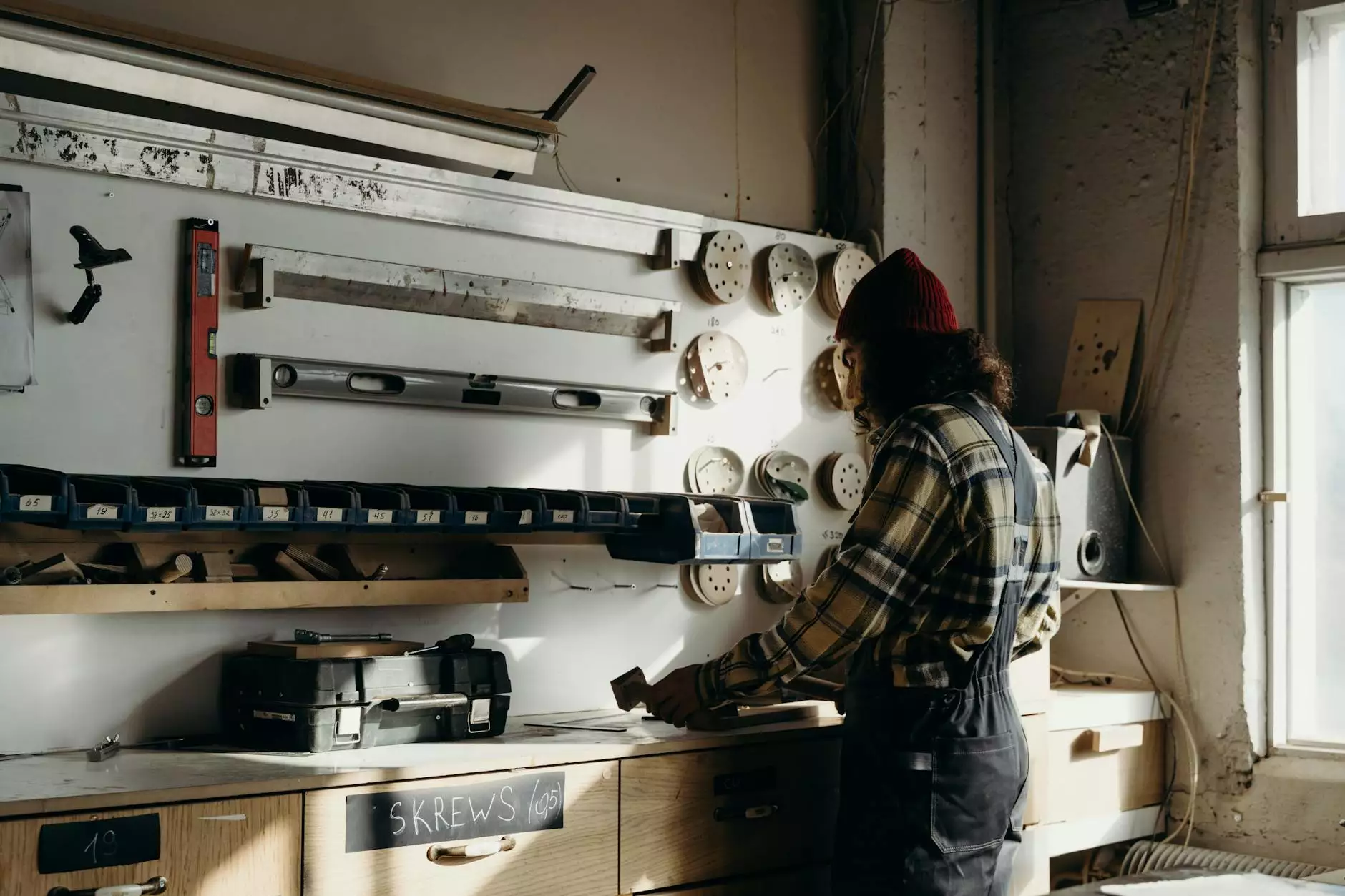
Plastic mold injection manufacturers are essential players in the contemporary manufacturing ecosystem. They are responsible for producing a wide array of components that are fundamental in numerous sectors, including automotive, consumer goods, electronics, and medical devices. This article delves deep into the world of plastic mold injection, highlighting its processes, benefits, applications, and the future of this critical industry.
Understanding Plastic Mold Injection
Plastic mold injection is a manufacturing process that involves the injection of molten plastic into a mold to create specific shapes and designs. This method is favored for its versatility, efficiency, and ability to produce high-quality components in large volumes.
The Injection Molding Process
The process of injection molding encompasses several stages:
- Material Preparation: The first step involves selecting the appropriate plastic resin, which is then dried and prepped for molding.
- Injection: The dried plastic is heated until it melts and is then injected into a mold at high pressure.
- Cooling: Once the mold is filled, the material is cooled to solidify into the desired shape.
- Demolding: After cooling, the mold opens, and the finished product is ejected.
- Finishing: Additional processes may include trimming, painting, or assembling parts as needed.
Types of Injection Molding
There are various methods of injection molding, allowing manufacturers to choose the best one based on their specific needs:
- Standard Injection Molding: The traditional method used for a wide range of products.
- Multi-Shot Injection Molding: Involves using multiple materials or colors in a single part.
- Gas-Assisted Injection Molding: Uses gas to create hollow sections within plastic parts, reducing weight and material costs.
- Insert Molding: Involves placing a substrate into the mold to be encased in plastic.
Benefits of Working with Plastic Mold Injection Manufacturers
Choosing to collaborate with plastic mold injection manufacturers comes with numerous advantages that enhance production efficiency and product quality:
Cost-Effectiveness
One of the primary benefits of plastic injection molding is its cost-effectiveness for large production runs. The initial setup cost can be high, but once the mold is created, the per-unit cost decreases dramatically. This makes it an ideal choice for mass production.
High Precision and Detail
Injection molding allows for intricate designs with tight tolerances, meaning that manufacturers can produce highly complex parts with high precision. This level of detail is crucial in industries such as automotive and medical, where precision is paramount.
Material Versatility
Plastic mold injection manufacturers can work with a wide variety of thermoplastics and thermosetting plastics. This versatility enables them to customize the materials according to the specific requirements of the application, whether durability, flexibility, or heat resistance is needed.
Reduced Waste
Injection molding is an efficient process that minimizes waste. The ability to reuse scrap material reduces environmental impact, making it a more sustainable choice for manufacturers today.
Applications of Plastic Mold Injection
The applications of plastic injection molding are extensive and span multiple industries:
- Automotive Industry: Production of dashboards, door panels, and other components.
- Consumer Goods: Creation of everyday products like containers, toys, and household items.
- Electronics: Manufacturing of housings for devices such as mobile phones and computers.
- Medical Devices: Development of components requiring high sanitary standards and precision, such as syringes and implantable devices.
The Role of DeepMould.net in the Injection Molding Ecosystem
As a leading player in this field, DeepMould.net serves the diverse needs of customers looking for quality plastic mold injection services. With a focus on innovation and quality, DeepMould.net stands out among plastic mold injection manufacturers by:
Offering Comprehensive Solutions
DeepMould.net provides end-to-end solutions from design to production and assembly, ensuring that clients receive a well-rounded service tailored to their needs. This approach enables efficient communication and coordination throughout the project life cycle.
Advanced Technology and Equipment
At DeepMould.net, investment in state-of-the-art technology and equipment is a priority. The company utilizes the latest machinery and tools in the industry, allowing for quick setup times and high production rates while maintaining quality standards.
Expertise and Experience
The team at DeepMould.net consists of skilled professionals with extensive experience in plastic mold injection. Their deep understanding of materials, design, and engineering principles ensures customer satisfaction and product excellence.
Future Trends in Plastic Mold Injection Manufacturing
The future of plastic mold injection manufacturing looks promising, with several trends set to shape the industry:
Automation and Industry 4.0
The integration of automation and smart technologies heralds a new era for manufacturing. With the rise of Industry 4.0, plastic mold injection manufacturers are adopting smart factories that utilize IoT, AI, and data analytics to optimize production processes.
Sustainable Practices
As the global push for sustainability grows stronger, manufacturers are looking at ways to reduce their carbon footprint. This includes using recycled materials, sustainable sourcing, and more efficient production methods.
Customization and Personalization
With the advent of advanced manufacturing technologies, the ability to customize products has become more accessible. Consumers increasingly demand personalized solutions, prompting plastic mold injection manufacturers to adapt their processes.
Conclusion
In conclusion, plastic mold injection manufacturers like DeepMould.net play a critical role in the modern manufacturing landscape. Their ability to produce high-quality, precise components efficiently and cost-effectively makes them invaluable to industries worldwide. As technology advances and consumer demands shift, these manufacturers are poised to rise to new challenges, ensuring they remain at the forefront of innovation and excellence in production.