Transforming Industries: The Role of a Premier Die Casting Mold Company
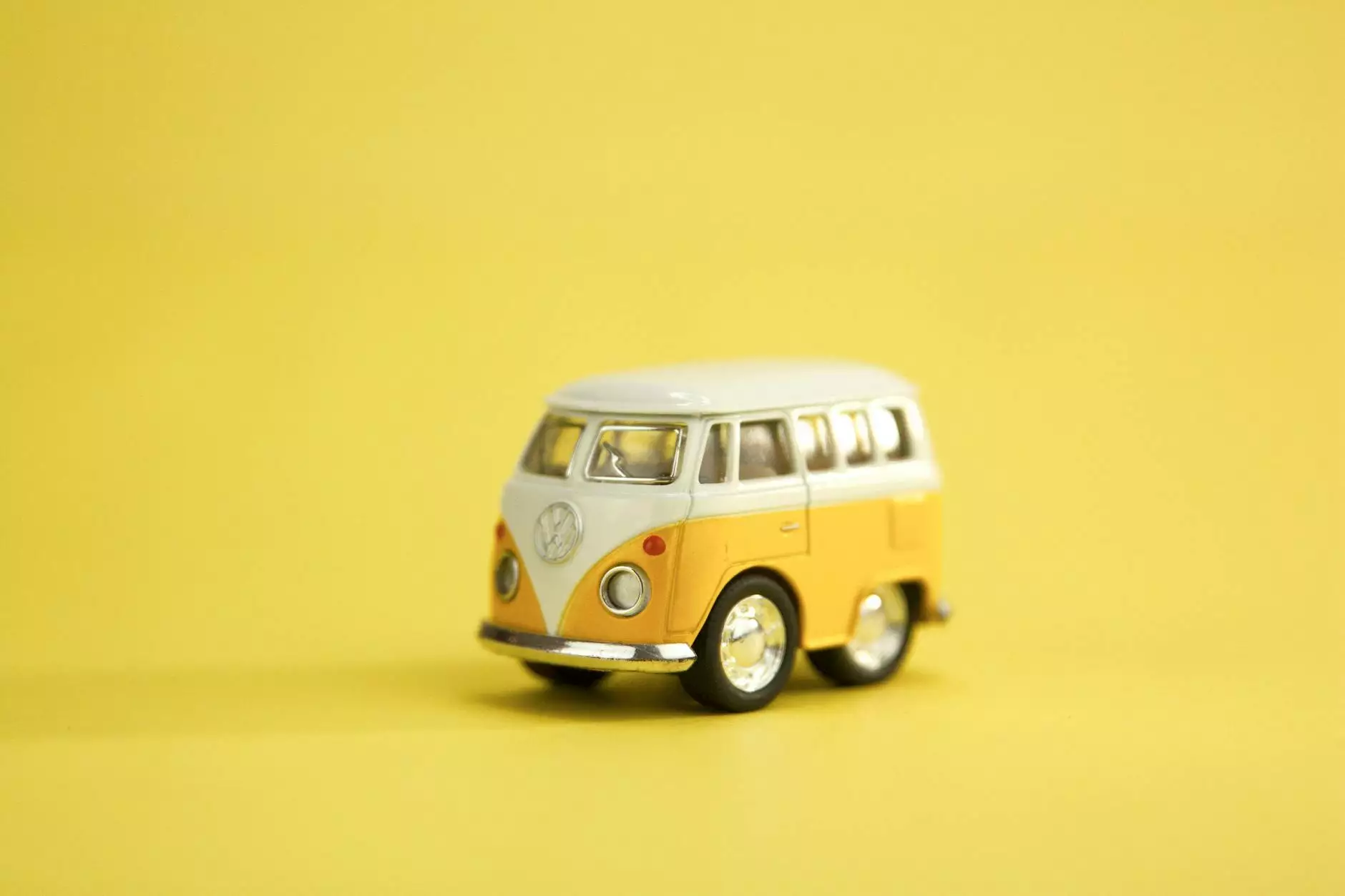
In the rapidly advancing world of manufacturing, precision, and efficiency are paramount. One sector that embodies these principles is die casting, particularly through the expertise of a die casting mold company. Businesses such as DeepMould.net are at the forefront of this revolutionary process, providing crucial support to a variety of industries, including automotive, aerospace, and consumer goods.
The Basics of Die Casting
Die casting is a manufacturing process that involves forcing molten metal into a mold cavity under high pressure. This method produces parts with exceptional detail and complexity, making it ideal for creating intricate shapes with minimal secondary finishing. The precision and consistency achieved through this process are unmatched, making it a preferred choice for manufacturers worldwide.
Why Choose a Professional Die Casting Mold Company?
Choosing the right die casting mold company can significantly impact the success of your manufacturing project. Here’s why partnering with a proficient company like DeepMould.net is essential:
- Expertise: With years of experience in the field, a skilled die casting mold company brings invaluable knowledge to the table, ensuring that every project is handled with care and precision.
- State-of-the-Art Technology: High-quality mold production requires advanced technology. A leading company will utilize the latest machinery and software to create molds that meet rigorous industry standards.
- Customization: Every project is unique. A reputable die casting mold company offers tailored solutions to meet the specific needs and requirements of each client.
- Quality Assurance: Rigorous testing and quality control processes ensure that the final products meet the highest standards of excellence and reliability.
- Cost Efficiency: By utilizing specialized techniques and efficient processes, a professional company can reduce production costs without sacrificing quality.
The Die Casting Process Explained
Understanding the die casting process is vital for manufacturers looking to optimize their production lines. Here’s a detailed breakdown:
- Mold Design: A skilled team designs the mold based on the specifications provided by the client. This stage is critical, as proper design influences the final product's quality and cost.
- Melt Preparation: Raw metal is melted in a furnace at extreme temperatures, ensuring it is in a liquid state before injection.
- Injection: The molten metal is injected into the mold under high pressure, filling even the smallest details effectively.
- Cooling: Once the mold is filled, the metal cools and solidifies, taking the shape of the mold.
- Mold Release: After cooling, the mold is opened, and the finished product is ejected. This step requires care to avoid damaging the delicate features of the casting.
- Finishing: The final product may undergo various finishing processes, including trimming, polishing, and painting, to meet the specifications required by the client.
Applications of Die Casting
The versatility of die casting allows for its application across numerous sectors. Some of the most common applications include:
- Automotive Components: Many components in vehicles, such as engine blocks, transmission cases, and structural parts, are produced using die casting.
- Aerospace Parts: The aerospace industry relies heavily on die casting for producing lightweight but strong components used in aircraft and spacecraft.
- Consumer Electronics: Electronic devices often require intricate housings and parts that can be efficiently created through die casting.
- Healthcare Equipment: Precision in manufacturing medical devices is crucial, and die casting provides the tolerances needed for such applications.
The Benefits of Choosing DeepMould.net
As a leading die casting mold company, DeepMould.net offers several advantages:
DeepMould.net stands out due to its commitment to excellence and innovation. Here are several reasons to choose us:
- In-Depth Consultation: We work closely with you to understand your needs and deliver the best possible design for your die casting project.
- High-Quality Materials: Only premium materials are used in mold construction to ensure durability and performance.
- Fast Turnaround Times: Our efficient production processes enable us to deliver your products in a timely manner without compromising quality.
- Comprehensive Services: From mold design to final product delivery, we offer end-to-end solutions for all your die casting needs.
- Continuous Support: We provide ongoing support and service even after the initial delivery, ensuring long-term satisfaction.
Case Studies: Success Through Collaboration
We take pride in our collaborative approach that demonstrates the success of our partnerships. Here are a couple of case studies showcasing our impact:
Case Study 1: Automotive Innovations
A leading automotive manufacturer approached DeepMould.net to produce a complex engine component. Utilizing our state-of-the-art mold design technology, we created a mold that enabled them to reduce weight while improving strength. The result was a successful product launch that enhanced vehicle performance and efficiency.
Case Study 2: Aerospace Excellence
In another instance, a prominent aerospace company needed precision components for an upcoming aircraft model. Through rigorous quality assurance processes and high-quality materials, the components produced were not only lightweight but also met the stringent requirements of aviation standards, ensuring safety and reliability in flight.
The Future of Die Casting
As technology continues to evolve, so does the landscape of die casting. Innovations in additive manufacturing, artificial intelligence, and automation are set to transform the industry further. Companies like DeepMould.net are investing in these technologies to enhance mold production, optimize processes, and reduce environmental impacts.
Adopting green practices and focusing on sustainability is becoming increasingly important. The future die casting molds will likely be lighter, more efficient, and environmentally friendly, reflecting the industry's commitment to responsible manufacturing.
Conclusion
The expertise and innovation provided by a top-tier die casting mold company like DeepMould.net are essential for any business looking to thrive in the competitive landscape of manufacturing. With our commitment to quality, advanced technology, and customer satisfaction, we are not just molding metal; we are shaping the future of industry.
For businesses aiming to streamline their production processes and enhance their product quality, there’s no better partner than a dedicated die casting mold company that understands the nuances of the market. Choose DeepMould.net for your die casting needs and experience the difference today!