Understanding China Die Casting Manufacturers and Their Impact on the Industry
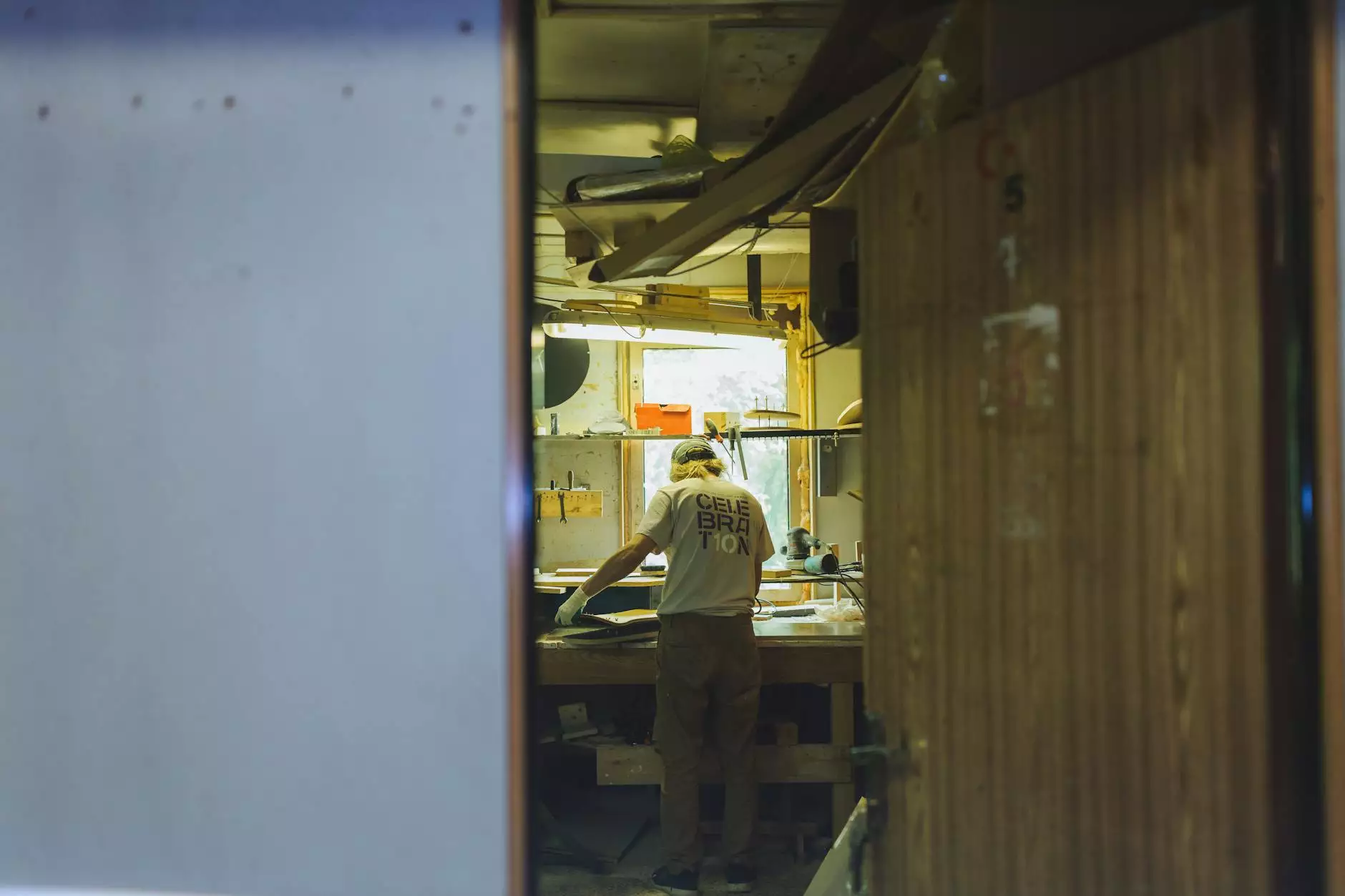
The rise of China die casting manufacturers has significantly altered the landscape of the global manufacturing sector. With innovations in technology, substantial cost reductions, and a wealth of experience, these manufacturers are at the forefront of producing high-quality, precision-engineered components.
What is Die Casting?
Die casting is a manufacturing process that involves forcing molten metal into a mold cavity under high pressure. This method facilitates the creation of intricate parts with tight tolerances, making it a favored choice in various industries, including automotive, aerospace, electronics, and consumer goods.
The Advantages of Working with China Die Casting Manufacturers
When it comes to sourcing die-casted components, China die casting manufacturers offer a multitude of advantages:
- Cost Efficiency: Labor costs in China are typically lower than in many Western countries, allowing for reduced production costs.
- Advanced Technology: Many Chinese manufacturers have invested heavily in modern die casting technologies, enabling them to produce parts with greater accuracy and efficiency.
- Scalability: With their extensive infrastructure and workforce, Chinese manufacturers can scale production quickly to meet the demands of large orders.
- Diverse Material Options: Chinese die casting factories typically work with a variety of materials, including aluminum, zinc, and magnesium alloys, providing flexibility based on specific project requirements.
- Rapid Prototyping: Many leading manufacturers in China can offer rapid prototyping services, allowing businesses to create and test prototypes quickly.
The Die Casting Process Explained
The die casting process can be broken down into several key stages:
1. Mold Creation
In this initial phase, a mold (or die) is created to reflect the design specifications of the part. The mold is typically made from hardened steel and can withstand the high pressures involved in the casting process.
2. Melting the Metal
Next, the chosen metal is heated in a furnace until it reaches a liquid state. For aluminum die casting, temperatures can reach around 660°C (1220°F).
3. Injection into the Die
Once the metal is molten, it is injected into the mold at high pressure. This ensures that the liquid metal fills all cavities of the mold before solidifying.
4. Cooling
As the metal begins to cool, it solidifies into the desired shape. Cooling times vary based on part thickness and the type of metal used.
5. Ejection from the Die
Once cooled, the newly-formed part is ejected from the die. This step must be carefully managed to prevent damage to the part or the die itself.
6. Finishing Processes
After ejection, additional finishing processes like machining, sanding, or polishing may be necessary to meet tight tolerances and surface finish requirements.
The Role of Quality Assurance in Die Casting
Quality assurance is paramount in die casting to ensure that the final products meet industry standards and customer expectations.
Inspection Techniques
China die casting manufacturers employ various inspection techniques, including:
- Visual Inspections: Checking for surface defects and overall appearance.
- Dimensional Checks: Using tools like calipers and gauges to measure critical dimensions.
- Non-Destructive Testing: Techniques such as ultrasonic testing and X-rays help identify internal issues without damaging the part.
The Future of Die Casting in China
The future of China die casting manufacturers looks promising, with advancements in technology and an increasing demand for lightweight and high-performance materials. Below are some key trends shaping the future:
1. Sustainability Practices
As environmental concerns continue to grow, die casting manufacturers in China are adapting by implementing more sustainable practices, such as recycling waste materials and optimizing energy consumption.
2. Automation and Industry 4.0
Automation technologies, including robotics and artificial intelligence, are being increasingly integrated into the die casting process, enhancing precision and reducing production times.
3. Customization and Flexibility
Manufacturers are focusing on customization, providing tailored solutions that meet the specific requirements of different industries and clients. This trend is complemented by advancements in 3D printing and rapid prototyping.
Choosing the Right China Die Casting Manufacturer
When selecting a China die casting manufacturer, there are several factors to consider:
- Experience and Reputation: Choose manufacturers with a proven track record and positive customer feedback.
- Certifications: Look for manufacturers with relevant industry certifications to ensure compliance with quality standards (e.g., ISO 9001).
- Technical Capabilities: Assess the technical capabilities and equipment available to ensure they align with your project requirements.
- Communication: Ensure that the manufacturer has effective communication practices in place to facilitate seamless collaboration.
- After-Sales Support: Consider how the manufacturer handles post-production support, including warranty policies and part replacement services.
Conclusion
In conclusion, the significance of China die casting manufacturers cannot be overstated. Their ability to deliver high-quality, cost-effective solutions tailored to a wide range of industries has established them as vital players in the global manufacturing arena. As technology evolves and sustainability becomes more critical, these manufacturers are well-positioned to meet future challenges and continue to thrive.
For businesses looking to leverage the benefits of die casting, partnering with a reliable manufacturer in China can lead to significant competitive advantages. As you explore the options, focus on those that can provide a combination of quality, reliability, and innovation to ensure your business thrives in an increasingly competitive market.
Contact Us
To learn more about how Deep Mould can assist you with your die casting needs, explore our services on our website or contact us directly!