Architectural Wood Model Maker: Bridging Artistry and Precision in Architecture
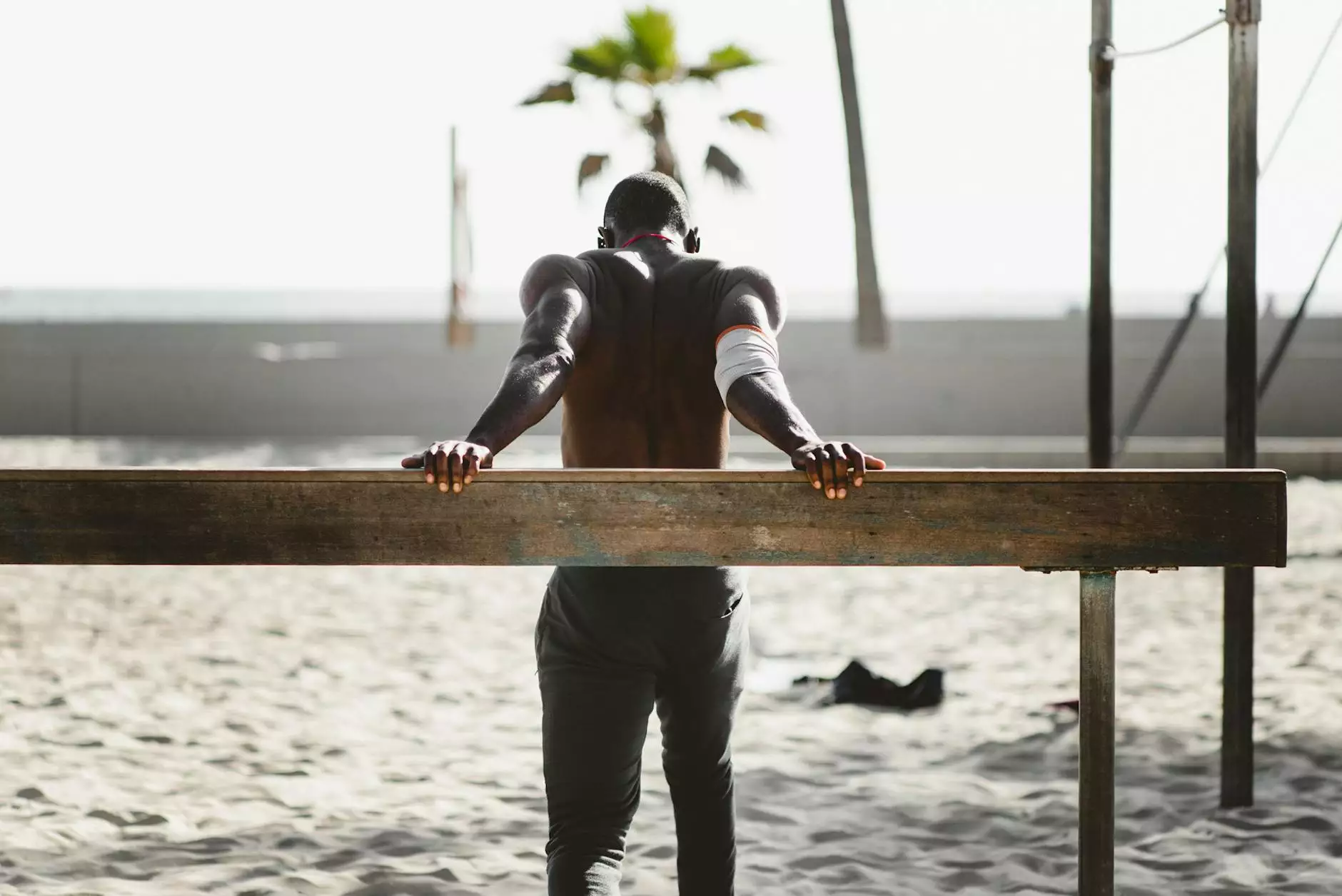
In the realm of architecture, the importance of visual representation cannot be overstated. An architectural wood model maker serves as a vital link between concepts and reality, transforming ideas into tangible architectural models. This comprehensive exploration delves into the fascinating work of architectural wood model makers, their methods, advantages, and the diverse applications of their craft in the architectural landscape.
The Essence of Architectural Wood Model Making
Architectural model making is a time-honored tradition that combines artistry and technical skill. At its core, an architectural wood model maker is tasked with creating accurate and aesthetically pleasing scale models made primarily from wood. These models are not just replicas; they are powerful tools for communication, enabling stakeholders to visualize the spatial dynamics and design intricacies of a building before it is constructed.
Why Choose Wood for Architectural Models?
Wood is a preferred medium among many model makers for several reasons:
- Aesthetic Appeal: Wood possesses a natural beauty that lends warmth and elegance to models.
- Workability: It is easy to cut, shape, and finish, allowing for detailed craftsmanship.
- Durability: With proper care, wooden models can last for decades.
- Eco-Friendliness: Sustainable sourcing makes wood an environmentally responsible choice.
The Role of an Architectural Wood Model Maker
The role of an architectural wood model maker encompasses a variety of responsibilities:
1. Conceptualization and Design Collaboration
The process begins with close collaboration with architects and designers. The model maker interprets the architect’s vision, translating drawings and concepts into three-dimensional representations. This stage often involves discussions about scale, detail, and materials, ensuring the model reflects the intended design accurately.
2. Selection of Materials
While wood is the primary material, the choice of type (such as balsa, birch, or basswood) is crucial. Each variety has distinct properties that affect the model's outcome. For instance, balsa wood is lightweight and easy to cut, making it ideal for intricate designs, whereas birch provides sturdiness and an elegant finish.
3. Crafting the Model
Using advanced tools and techniques, the model maker meticulously constructs the model. This process includes:
- Cutting: Precision cutting tools are employed to ensure accurate dimensions.
- Assembling: Pieces are glued and fastened to create a stable structure.
- Finishing: Sanding, staining, and sealing enhance the model's aesthetics and protect the wood.
4. Detailing and Presentation
After the basic structure is complete, detailing adds life to the model. Features such as windows, doors, and landscape elements are crafted to enhance realism. The final presentation often involves custom bases or display cases to showcase the model effectively during client meetings or exhibitions.
The Advantages of Architectural Wood Models
Opting for wood models in architectural presentations offers several compelling advantages:
- Clarity of Design: A physical model allows clients to grasp complex designs effortlessly.
- Enhanced Communication: Models serve as a common language among architects, clients, and contractors.
- Iterative Design Improvements: Models can be easily modified, enabling rapid testing of design alterations.
- Tactile Experience: Clients can engage with the model physically, leading to more impactful discussions.
Applications of Wooden Architectural Models
The versatility of architectural wood models extends across various domains, including:
1. Residential Projects
For residential architecture, detailed wood models help homeowners visualize their future spaces, facilitating discussions about design choices, materials, and layouts.
2. Commercial Developments
In commercial architecture, models play a crucial role in external presentations and marketing materials. They can be used in pitch meetings with investors and stakeholders, illustrating the potential impact of the development on its surroundings.
3. Urban Planning
Urban planners utilize scale models to simulate the relationship between new structures and existing environments, helping to identify potential issues with zoning, traffic, and aesthetics.
The Future of Architectural Wood Model Making
As technology advances, architectural wood model makers are increasingly integrating digital tools with traditional craftsmanship. The use of CAD software, laser cutting, and 3D printing is revolutionizing the way models are designed and constructed. However, the human touch in handcrafted wood models retains a value that machines cannot replicate. The future lies in a harmonious blend of craftsmanship and technology, enhancing the architectural design process further.
Choosing the Right Architectural Wood Model Maker
Selecting the right architectural wood model maker is crucial for the success of any project. Consider the following factors:
- Experience: Look for a model maker with a proven track record in creating highly detailed and accurate models.
- Portfolio: Review their previous work to assess their style, attention to detail, and craftsmanship.
- Collaborative Approach: Choose someone who values communication and collaboration with architects and clients.
- Technology Proficiency: Ensure they are well-versed in both traditional methods and modern technologies.
Conclusion
In conclusion, the role of an architectural wood model maker is indispensable in the architectural field. Their ability to transform abstract ideas into tangible representations not only aids in communication and understanding but also enriches the overall design process. As architecture continues to evolve, so too will the techniques and technologies that model makers employ. Investing in high-quality wooden models is an investment in clarity, vision, and artistic excellence in the architectural world.
For more insights and services, visit us at architectural-model.com.