Unlocking Efficiency with Rapid Prototype Injection Molds
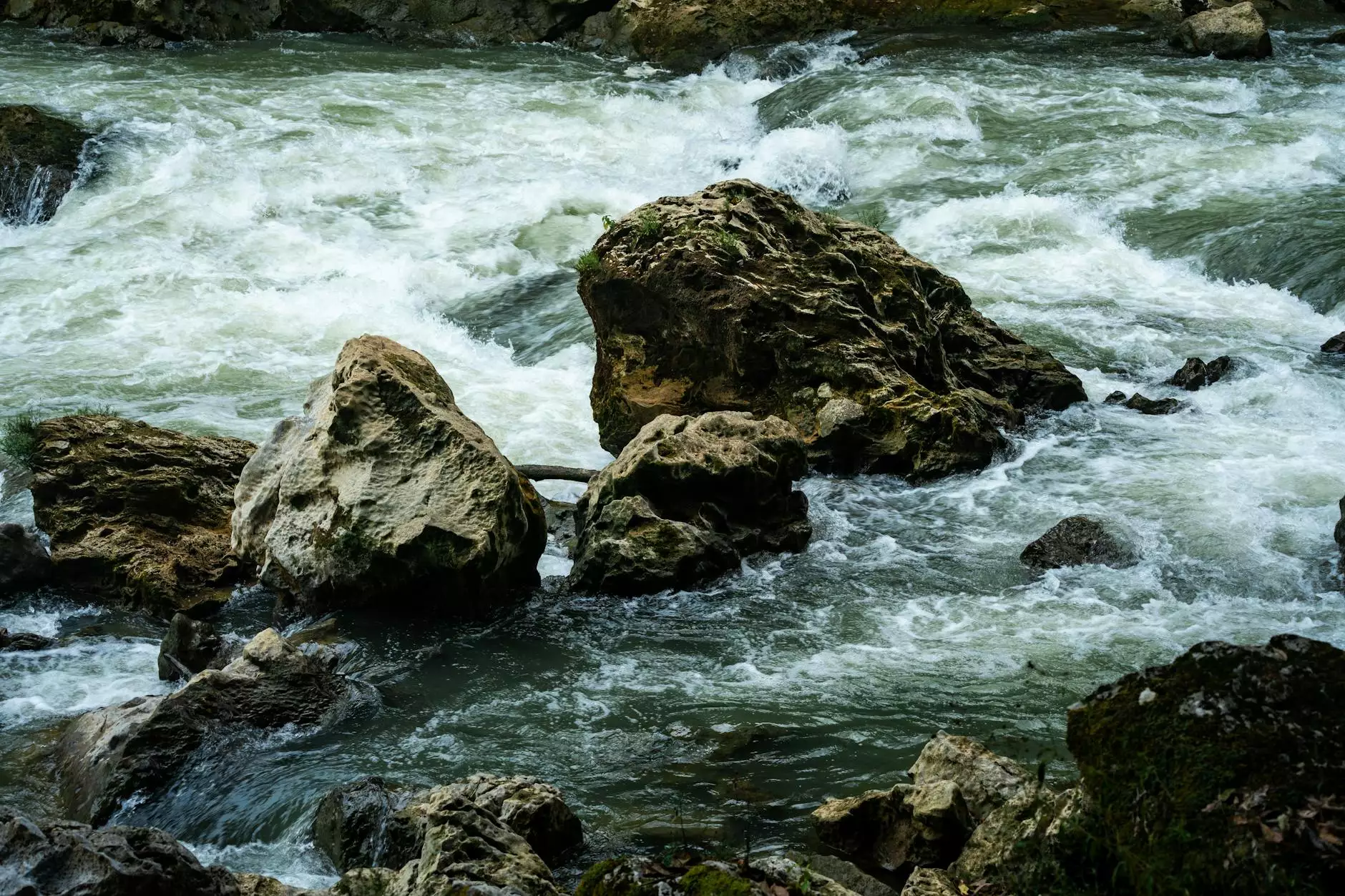
In today's rapidly evolving business landscape, innovation is key to staying ahead of the competition. One of the most significant advancements in manufacturing technology is the use of rapid prototype injection molds. These molds enable businesses, particularly within the realm of metal fabricators, to streamline their production processes, reduce costs, and accelerate time-to-market. This article delves into the various aspects of these molds, highlighting their importance, advantages, and applications in modern manufacturing.
The Basics of Injection Molding
Injection molding is a manufacturing process that involves injecting molten material into a mold to create precise shapes and forms. Traditionally associated with thermoplastics, this method has expanded to include various materials, including metals. Rapid prototype injection molds are specifically designed for quick turnaround times, allowing companies to produce test samples or small batches of a product quickly and efficiently.
What Are Rapid Prototype Injection Molds?
Rapid prototype injection molds are specialized molds used to create prototypes or low-volume production runs using injection molding techniques. The primary purpose of these molds is to facilitate the fast and efficient testing of designs before full-scale manufacturing begins. This process is invaluable for businesses that prioritize innovation and customer feedback in their product development cycles.
Key Features of Rapid Prototype Injection Molds
- Speed: These molds allow for rapid production of prototypes, significantly reducing the cycle time compared to traditional injection molds.
- Cost-Effectiveness: By utilizing lighter materials and simpler construction, rapid prototype molds can be produced at a fraction of the cost of full-production molds.
- Flexibility: Designed for iterative testing, rapid prototype molds support modifications in design without significant retooling costs.
- Precision: The process ensures high accuracy in the production of complex geometries, making it ideal for precise applications.
Advantages of Using Rapid Prototype Injection Molds
The benefits of incorporating rapid prototype injection molds into your production workflow are manifold:
1. Accelerated Time-to-Market
In a hyper-competitive market, being the first to introduce a product can provide a significant advantage. Rapid prototype molds enable businesses to quickly create prototypes, allowing them to test, evaluate, and refine their products in real-time. This speed not only enhances the development process but also allows companies to gather customer feedback sooner, leading to better end products.
2. Enhanced Collaboration
Rapid prototyping fosters collaboration among design, engineering, and marketing teams. By producing early models, all stakeholders can visualize the product, discuss modifications, and make informed decisions to improve the design before mass production begins. This collaborative approach reduces the risk of costly changes later in the process.
3. Reduced Development Costs
Using rapid prototype injection molds can significantly lower development expenses. The cost savings come from minimizing the need for expensive full-scale production molds until the final design is approved, reducing wasted materials and resources during the design phase.
4. Improved Product Quality
By allowing for thorough testing and revisions during the prototype stage, rapid prototype injection molds contribute to higher-quality final products. Companies can experiment with materials and designs, ensuring that the best possible version goes into production.
Applications of Rapid Prototype Injection Molds
The versatility of rapid prototype injection molds allows them to be used across various industries. Here are some applications where these molds are making a significant impact:
1. Automotive Industry
In the automotive sector, rapid prototyping is crucial for developing new parts and systems. Companies utilize prototype molds to create functional parts for testing fit, form, and function before full-scale production, reducing the risk of errors in costly final production runs.
2. Consumer Electronics
Consumer electronics require rapid iterations to keep up with technological advancements. Rapid prototype injection molds are used to print cases, components, and prototypes for new devices, ensuring products meet design specifications and consumer needs.
3. Medical Devices
The medical industry relies on precision and functionality. Rapid prototyping helps in developing surgical instruments, implants, and housings that must meet stringent regulatory requirements while allowing for preliminary testing and evaluations.
4. Aerospace and Defense
In aerospace and defense, prototypes are vital for ensuring performance and safety standards. Rapid prototyping provides the speed and accuracy needed to develop parts that will be subjected to rigorous testing conditions.
Choosing the Right Partner for Rapid Prototyping
For businesses looking to implement rapid prototype injection molds into their development process, selecting the right manufacturing partner is crucial. Here are some tips for finding the right fit:
1. Assess Experience and Expertise
Look for a partner with a proven track record in rapid prototyping and injection molding. Their experience will be beneficial in troubleshooting and optimizing processes.
2. Evaluate Technology and Capabilities
Different manufacturers employ various technologies and equipment. Ensure your partner uses the latest technology to produce high-quality prototypes efficiently.
3. Consider Customer Service and Support
Effective communication is essential throughout the prototyping process. Your partner should offer excellent customer service and support to address any issues that may arise.
4. Sample Their Work
Before committing, request samples of previous work. This will give you insight into their capabilities and the quality of their output.
Conclusion: Embracing the Future with Rapid Prototyping
As the landscape of manufacturing continues to evolve, embracing innovative technologies like rapid prototype injection molds is essential for staying competitive. They offer a unique solution for fast-paced industries that demand precision, quality, and cost-effectiveness. By integrating these tools into your workflow, you will not only streamline your development processes but also ensure that your products meet the evolving needs of your audience.
Ready to Get Started?
If your business is looking to explore the advantages of rapid prototype injection molds and how they can facilitate your next project, consider reaching out to DeepMould.net. Our expertise in manufacturing and commitment to quality will help you navigate the prototyping process, ensuring your product is market-ready efficiently and effectively.